Thank you!
The form has been successfully submitted.
Please find further information in your mailbox.
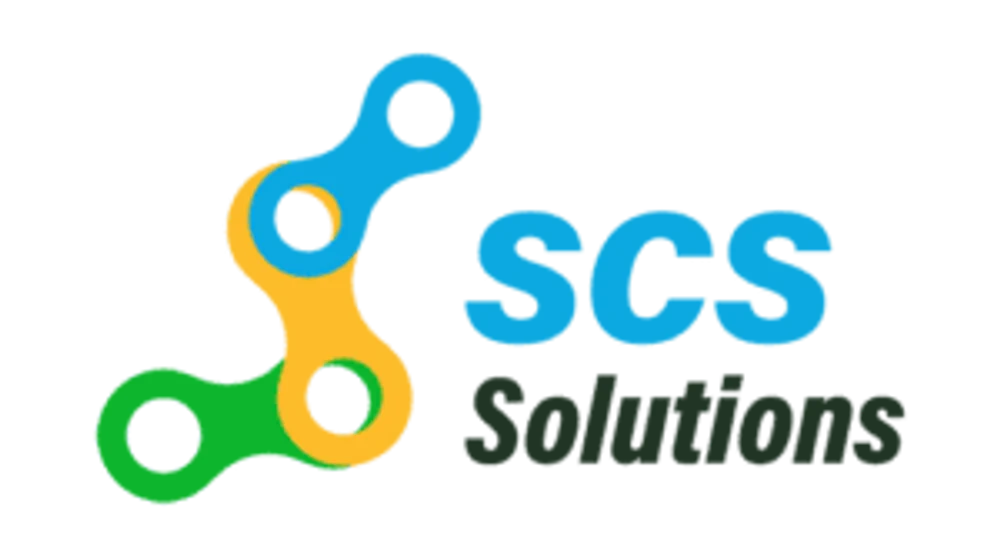
SCS Solutions, founded in 2019, is a global software development company with a team of over 100 IT experts. Leveraging 20+ years in software development and 30+ years in Supply Chain and Logistics, we offer tailored, innovative solutions for diverse business needs worldwide.
Warehouse Management System (WMS)Transportation Management System (TMS)Yard Management System (YMS)Material Resource Planning (MRP)Production Management System (PMS)E-commerce (Magento, Shoplify,…)Booking systemPoint of Sale (POS)Electronic Data Interchange (EDI)Digital TransformationInternet of Things (IoT)Automated System Operations (ASO)Asset Management System (ASM)
About us
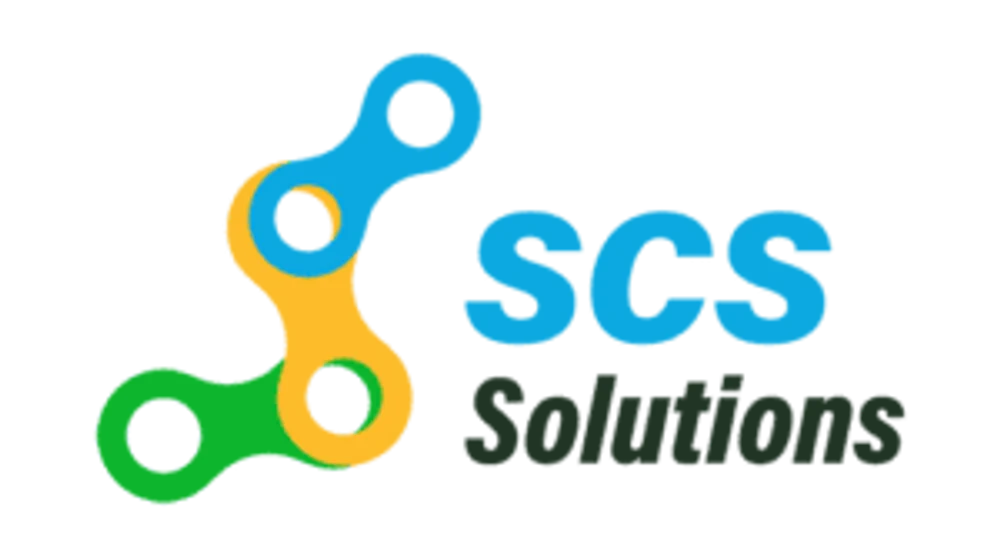
SCS Solutions, founded in 2019, is a global software development company with a team of over 100 IT experts. Leveraging 20+ years in software development and 30+ years in Supply Chain and Logistics, we offer tailored, innovative solutions for diverse business needs worldwide.
Services
All servicesWarehouse Management System (WMS)Transportation Management System (TMS)Yard Management System (YMS)Material Resource Planning (MRP)Production Management System (PMS)E-commerce (Magento, Shoplify,…)Booking systemPoint of Sale (POS)Electronic Data Interchange (EDI)Digital TransformationInternet of Things (IoT)Automated System Operations (ASO)Asset Management System (ASM)
Technologies
All technologies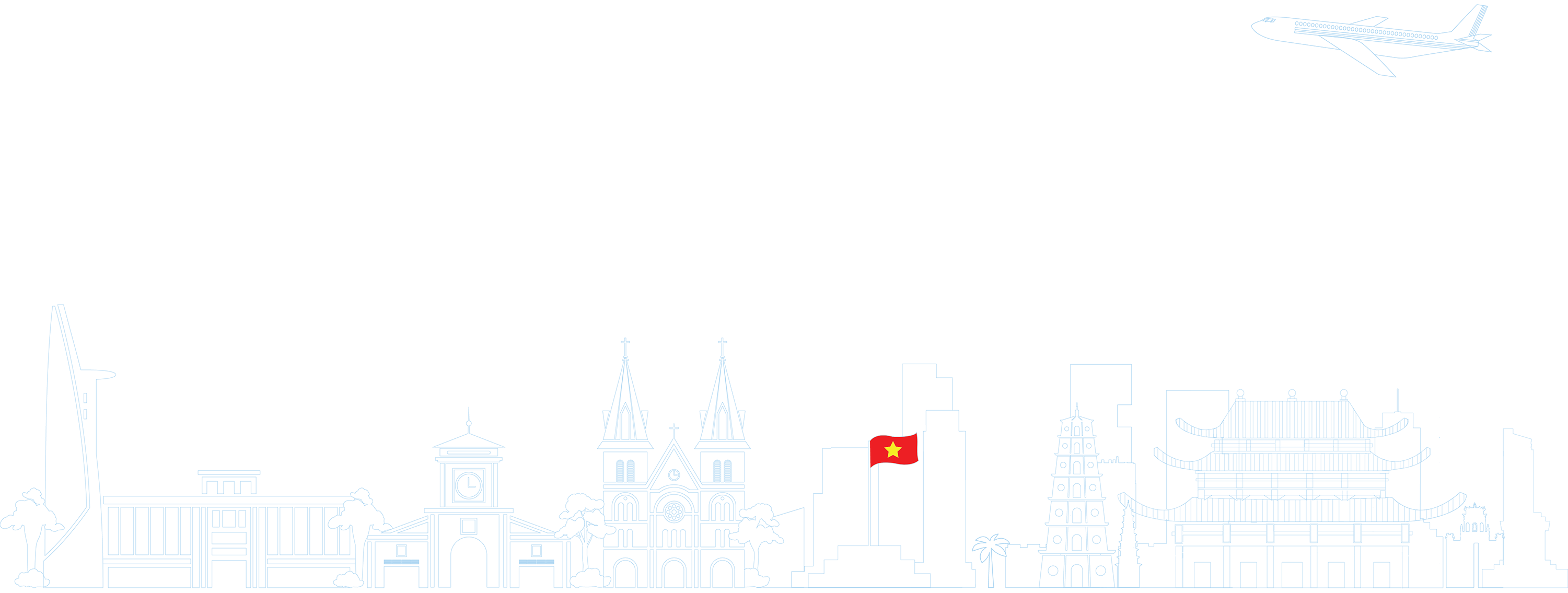
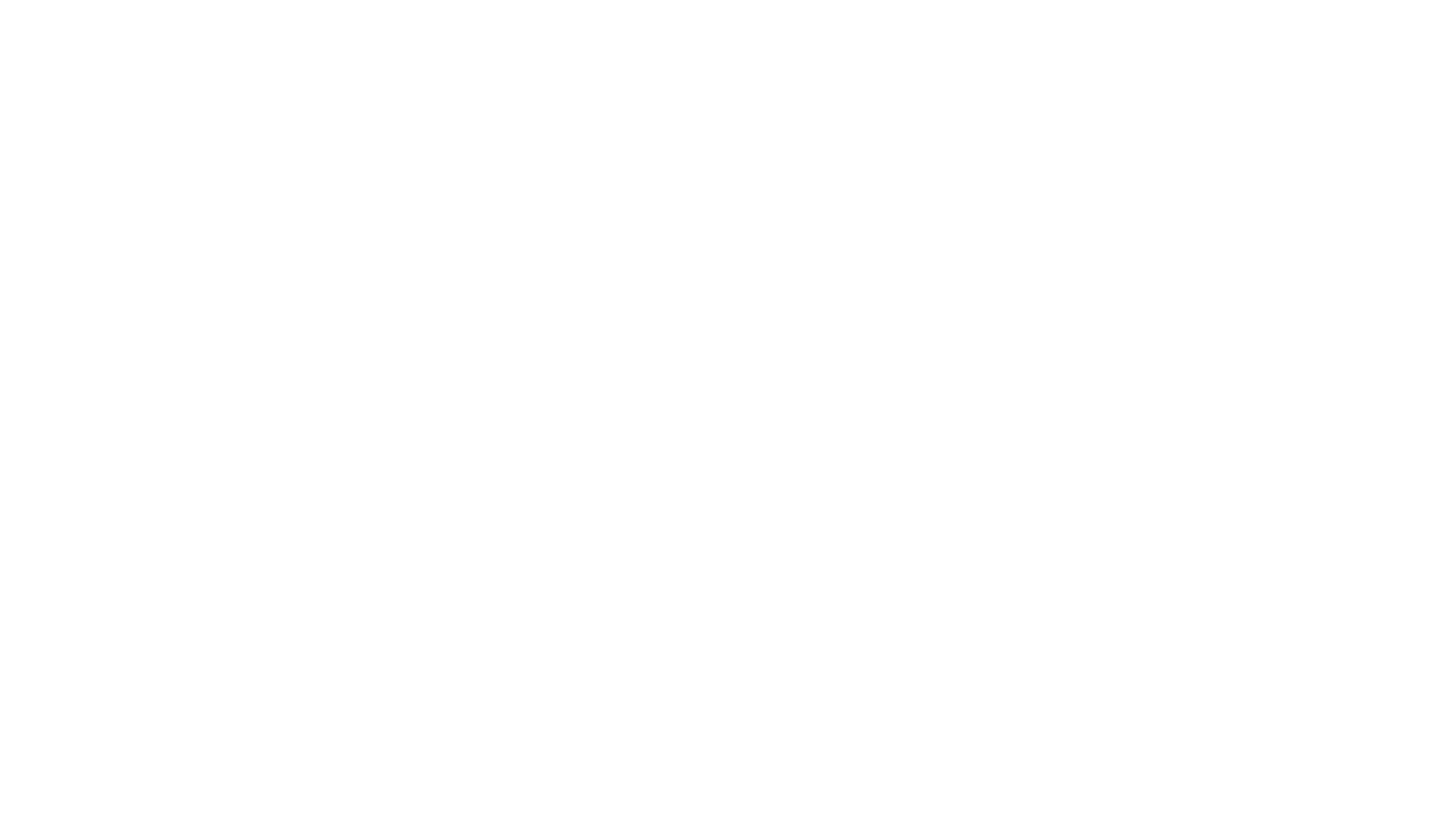
Let●s develop
software together!
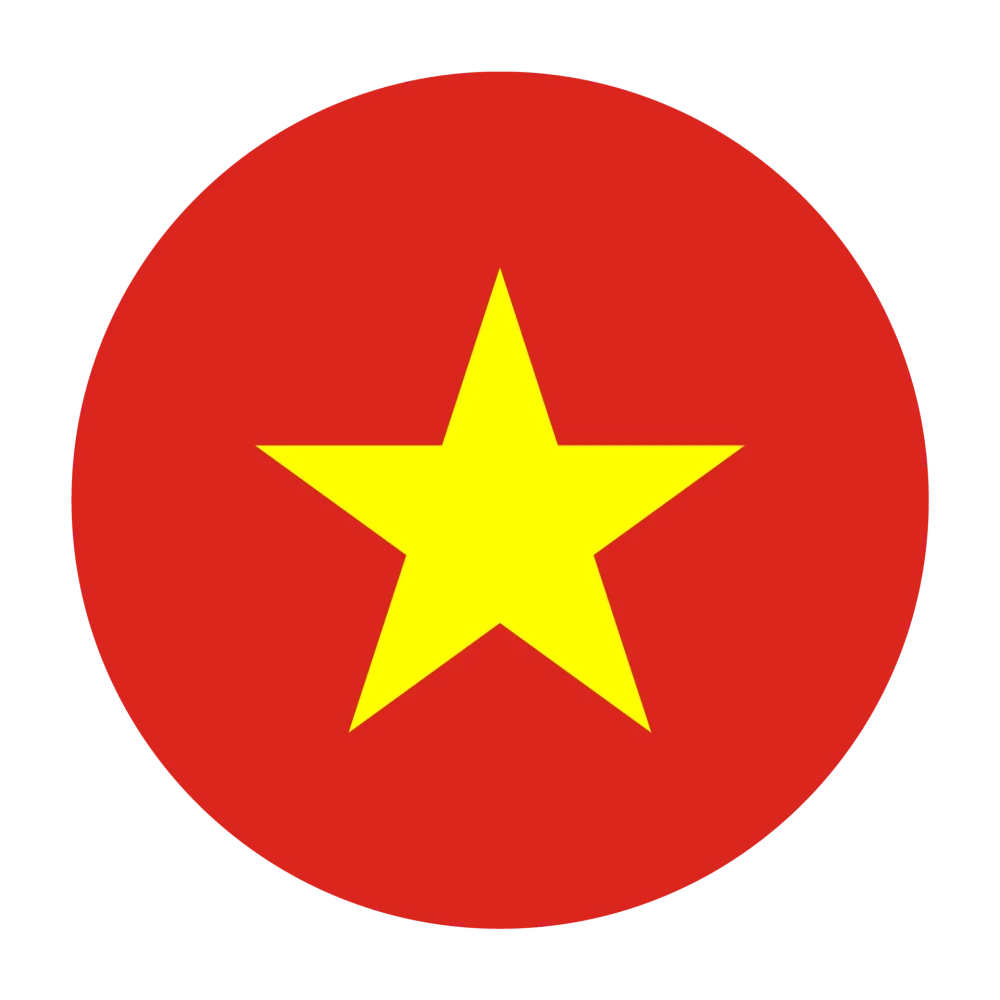
10/8 Phan Dinh Giot, Tan Son Hoa Ward, HCMC, Vietnam
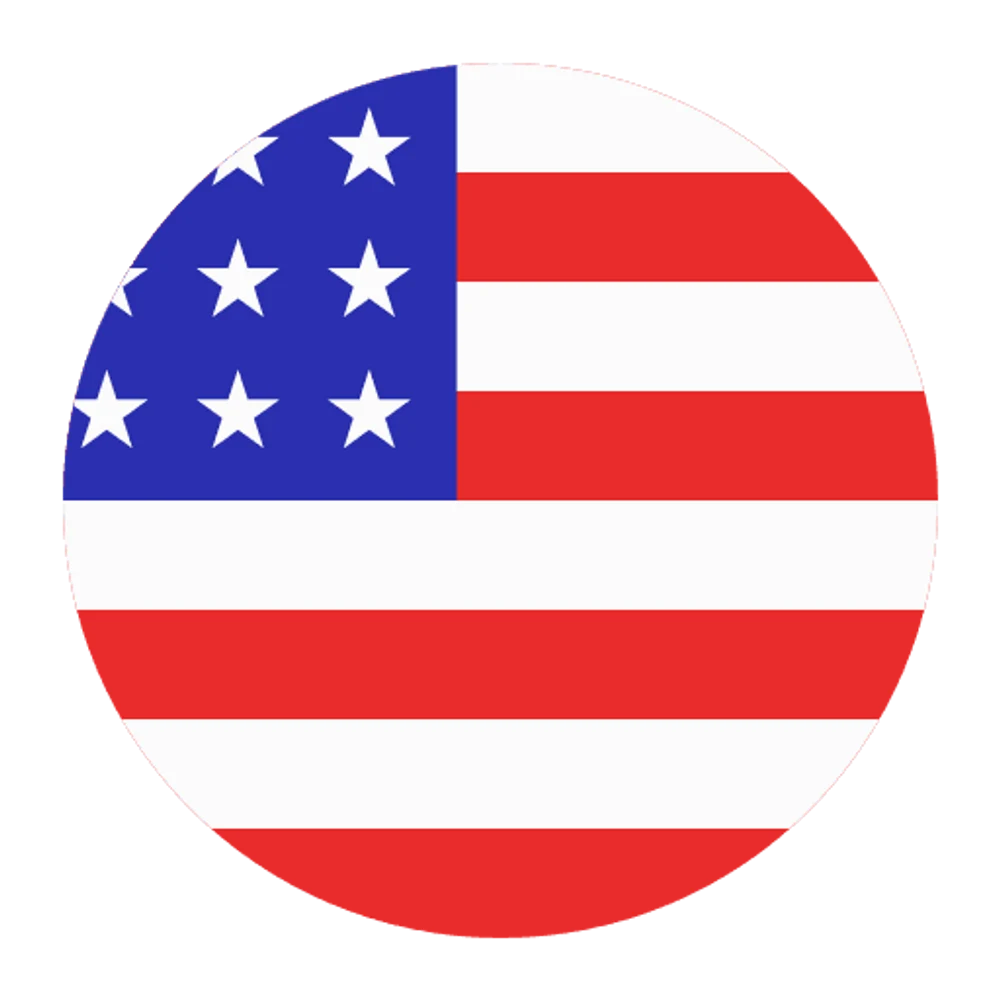
1160 Alum Creek Dr, Columbus, OH 43209
Email: info@scssolutions.io
Phone: (+84) 28 2202 2200
ServicesBig Data & Artificial IntelligenceDigital Transformation Consult & Development.Custom Software DevelopmentIT Staff Augmentation
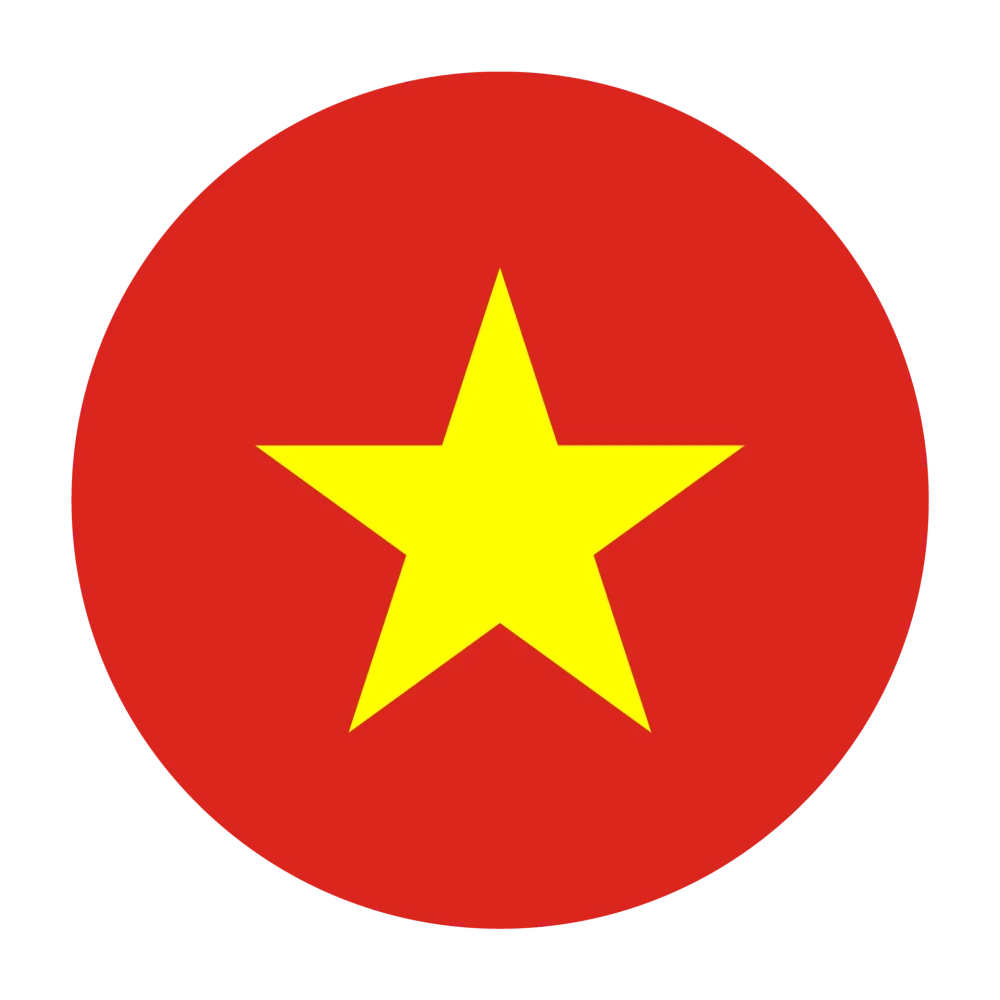
10/8 Phan Dinh Giot, Tan Son Hoa Ward, HCMC, Vietnam
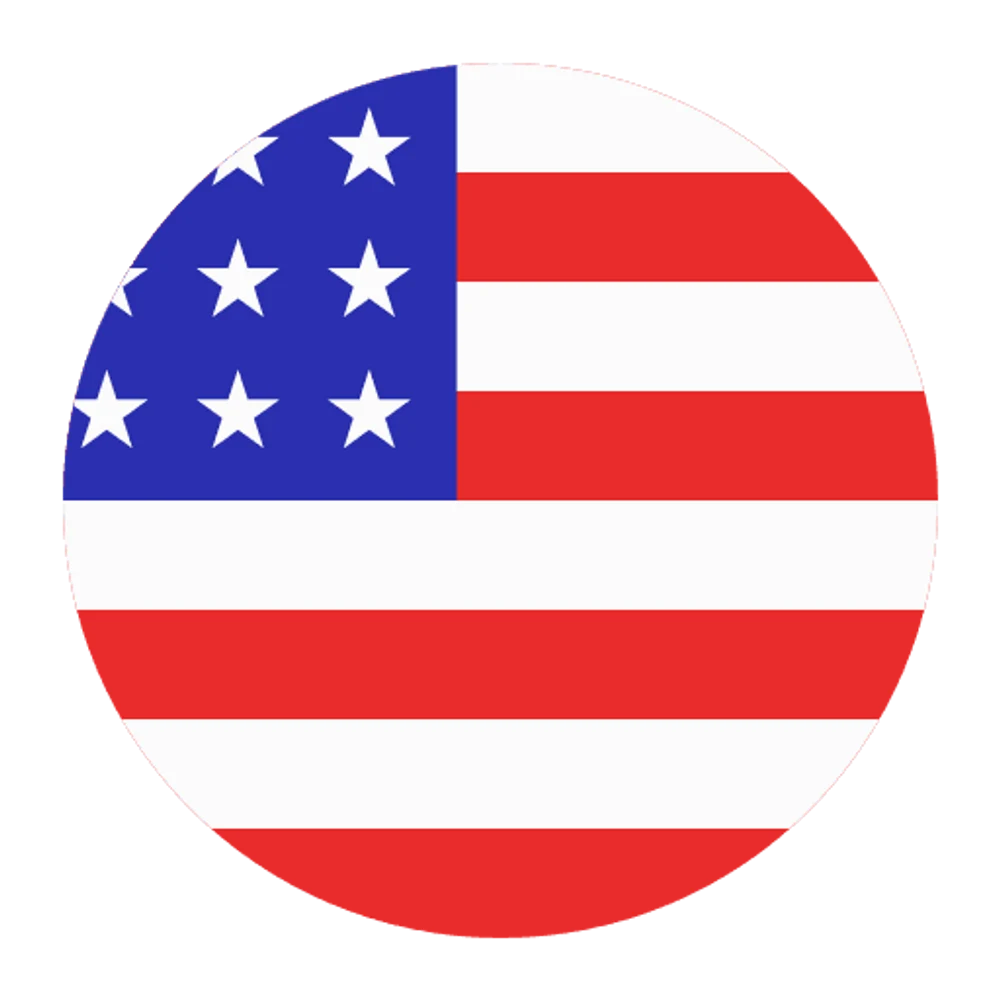
1160 Alum Creek Dr, Columbus, OH 43209
Email: info@scssolutions.io
Phone: (+84) 28 2202 2200